Henkel è in Italia da 90 anni ed entra nelle nostre case con marchi quali Loctite, Dixan o ancora Vernel a cui affianca altri prodotti votati all’industria. Il gruppo occupa 850 dipendenti e ha cinque sedi: gli uffici amministrativi di Milano e tre stabilimenti. Iniziamo questa intervista chiedendo a Luca Facheris, presidente Henkel Italia Operations, qual è il tratto distintivo che accomuna le aziende tedesche in fatto di standard produttivi. E che cosa distingue maggiormente sotto questo profilo Henkel Italia dalle altre realtà del nostro Paese. “I dati riferiti dalla Camera di Commercio Italo-tedesca parlano di quasi 2 mila aziende tedesche attive in Italia, con circa 170 mila dipendenti e un fatturato complessivo di oltre 70 miliardi di euro. In tutti i settori in cui sono presenti, dall’industria meccanica all’automotive, dalla chimica ai servizi, queste imprese si distinguono per gli standard molto elevati in fatto di efficienza, produttività e qualità. Anche Henkel ha standard decisamente alti e punta al miglioramento continuo. Con un pizzico di orgoglio, posso dire che chi lavora con noi, aziende partner e clienti, spesso resta stupito vedendo il livello di innovazione, qualità e sicurezza che abbiamo nei nostri siti”, spiega Facheris.
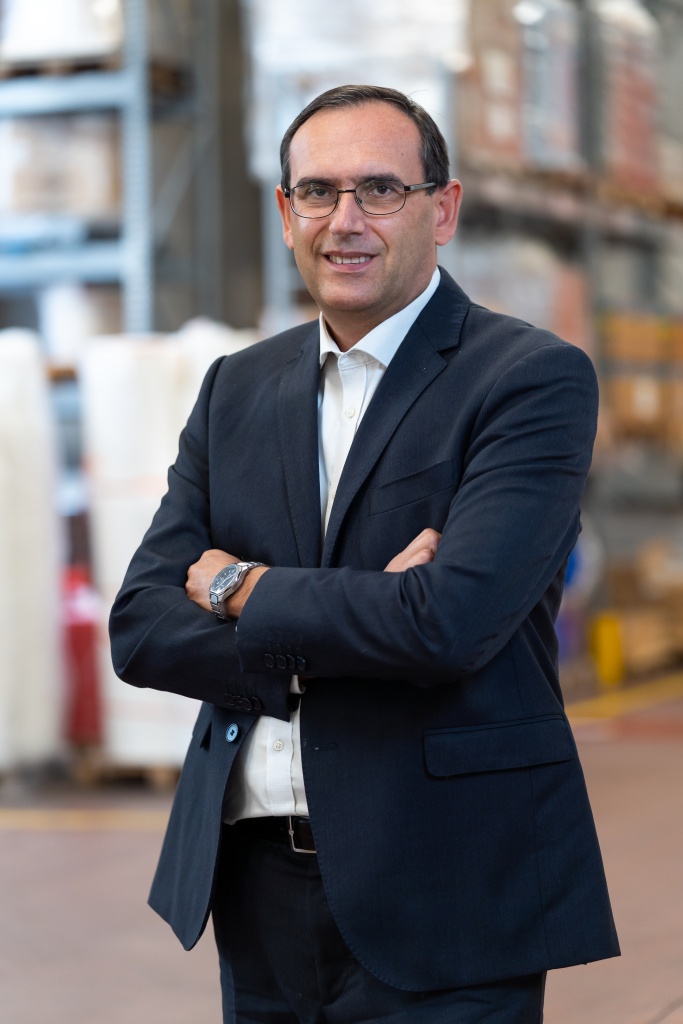
Henkel è conosciuta al grande pubblico per alcuni prodotti di largo consumo, quali le colle Pritt e i detersivi Dixan: ci sveli qualcosa dell’altra metà del business, quello degli adesivi industriali….
“Henkel si è affacciata al business degli adesivi per risolvere un problema molto concreto. Dobbiamo tornare in Germania, dopo la fine della Prima Guerra Mondiale, quando l’occupazione delle aree del Reno e della Ruhr rendeva complicato l’approvvigionamento di colla. L’azienda iniziò a sviluppare e produrre in autonomia adesivi per chiudere le confezioni di detersivi e cominciò a venderli ad alcune realtà della zona. Oggi, un secolo dopo, Henkel è leader mondiale nel mercato degli adesivi, dei sigillanti e dei rivestimenti per l’industria. Le nostre soluzioni entrano nella progettazione e nei processi produttivi di oltre 800 settori merceologici tra cui l’automotive, l’elettronica, il packaging e molti altri. È un mondo complesso ma affascinante, dove tecnologia, innovazione e sostenibilità sono determinanti”.
Vediamo ora il vostro sito produttivo di Casarile, visitato di recente dalla delegazione di 40 manager della Camera di Commercio Italo-tedesca. Henkel come intende sviluppare l’impianto anche in una ottica green? A fronte di quale investimento?
“Casarile è stato acquisito da Henkel nel 1988 ed è cresciuto fino a diventare uno dei nostri principali centri di competenza a livello mondiale nel settore degli adesivi a uso industriale, in particolare nelle tecnologie delle poliammidi, dei siliconi e delle resine epossidiche. I volumi di produzione sono triplicati negli ultimi 10 anni e oggi sono 2.200 le referenze che gestiamo tra prodotti finiti, materie prime e packaging. Una delle direzioni di sviluppo che stiamo seguendo prevede l’installazione di un nuovo reattore, che aumenterà del 20% la capacità produttiva delle poliammidi e l’ampliamento dell’area produzione epoxi che ci permetterà di aumentare la capacità produttiva sia di resine epossidiche che di siliconi speciali. Investiamo anche per ridurre costantemente l’impatto ambientale del sito: da quest’anno, con la messa in funzione del nuovo sistema di trigenerazione, Casarile è sostanzialmente autosufficiente dal punto di vista energetico perché riesce a produrre da sé l’elettricità, l’energia termica e frigorifera di cui ha bisogno”.
Qual è il filo conduttore che unisce Casarile agli altri poli produttivi del gruppo in Italia?
“In Italia abbiamo due stabilimenti dedicati agli adesivi industriali (Casarile, alle porte di Milano, e Zingonia, in provincia di Bergamo) e uno a Ferentino, in provincia di Frosinone, in cui produciamo detersivi per il bucato e le stoviglie. In tutti ritroviamo lo spirito pionieristico di Henkel che si traduce nell’innovazione continua e nella progressiva digitalizzazione di impianti e processi. Comune è anche l’attenzione alla sostenibilità, in linea con gli impegni globali dell’azienda in fatto di energia e impatto ambientale. Entro il 2030, tutti i nostri siti produttivi nel mondo, compresi quelli italiani, useranno il 100% di elettricità da fonti rinnovabili, con l’obiettivo di diminuire del 65% le emissioni di CO2 per tonnellata di prodotto rispetto al 2010”.
Vediamo in sintesi qualche esempio di ciascuno in termini di innovazione, sicurezza e green.
“Casarile è molto attivo nello sviluppo di tecnologie per il settore medicale, ad esempio ha messo a punto un adesivo termoplastico che viene utilizzato nella produzione dei sensori, applicabili sulla pelle, per il monitoraggio del glucosio nel sangue. Zingonia è stata invece il punto di riferimento per realizzare la formula degli adesivi a base acqua che ha contribuito ad accelerare l’abbandono delle cannucce di plastica per passare a quelle in carta, come previsto dalla normativa europea. In termini di sostenibilità, la stessa Zingonia è un ottimo esempio per quanto riguarda la gestione dei rifiuti: negli ultimi anni, grazie a vari progetti siamo riusciti a dimezzare la quantità di scarti che finisce in discarica. A Ferentino abbiamo messo in funzione un innovativo sistema di depurazione per migliorare la qualità delle acque reflue e favorirne il riuso, e anche qui abbiamo un impianto di trigenerazione per autoprodurre gran parte dell’energia di cui lo stabilimento ha bisogno”.
Contenuto consigliato